Reducing Downtime and Manual Work in a High-Cost Environment
One of North America’s most advanced automotive testing centers offers cutting-edge capabilities for aerodynamic and aeroacoustic testing, including rolling road systems, precision turntables, and the ability to generate wind speeds of up to 200 mph. These complex, high-performance systems generate critical data for vehicle development and validation—both for the facility’s parent company and external automotive clients.
With a per-minute operational cost approaching $70, inefficiencies in daily processes can quickly escalate into significant expenses. As the facility expanded third-party testing partnerships, leadership recognized the need to streamline technician workflows, improve process consistency, and reduce downtime.
Operational Cost Reduction
Improved Internal Experience
Scalable Digital Foundation
The Challenge
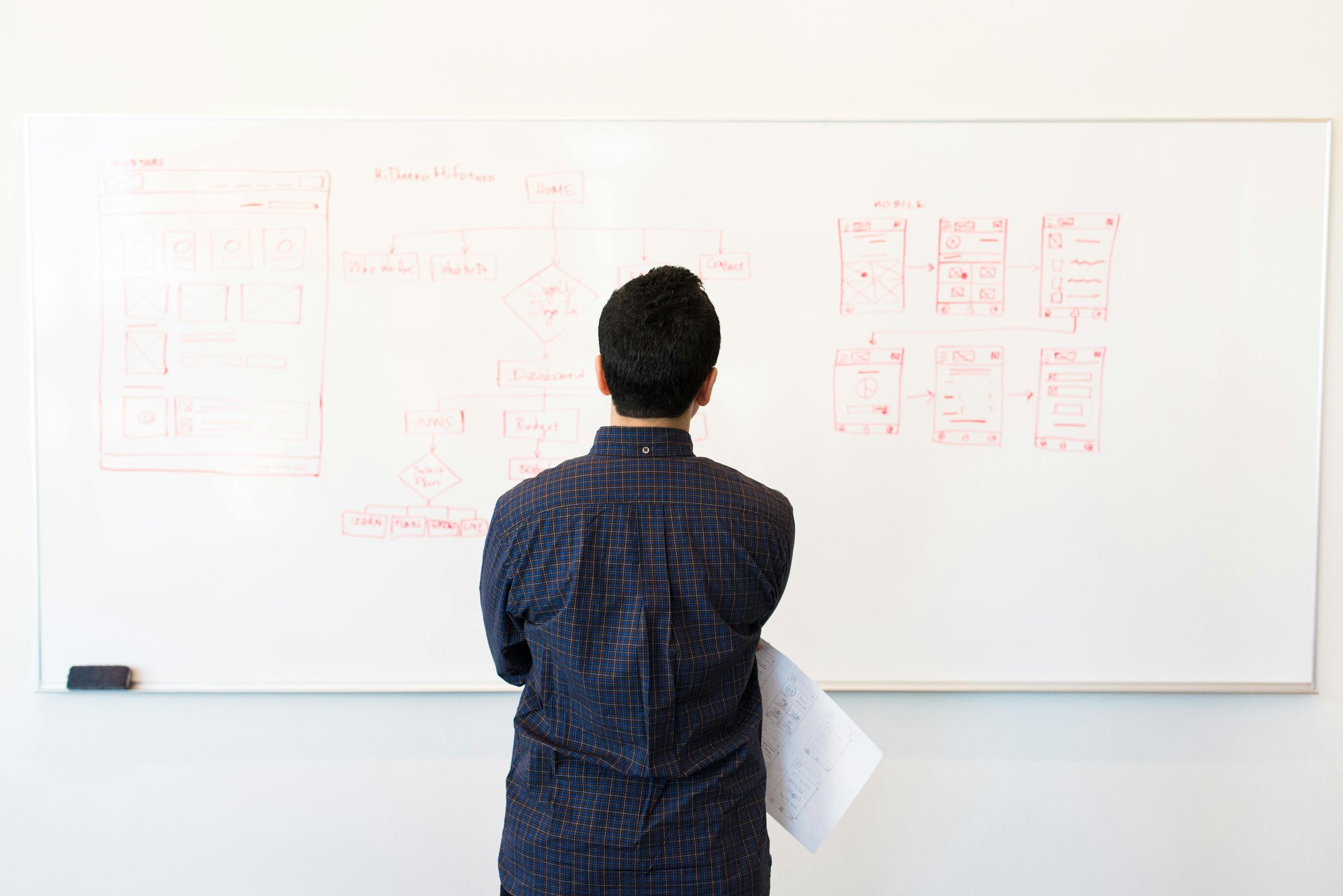
Complex Systems, Costly Inefficiencies
Technicians at the facility manage highly sensitive and detailed processes, including:
- Preparing complex testing equipment each morning
- Performing critical system checks and maintenance
- Executing precise, repeatable tests for both internal and external clients
- Responding to mechanical issues to avoid downtime
Despite the technical sophistication of the facility, outdated processes, manual tasks, and limited digital tools introduced inconsistencies and potential for costly errors.
The organization required an experienced technology partner to uncover hidden friction points, standardize operations, and propose digital solutions that would reduce technician burden and improve reliability.
Our Approach
Human-Centered Process Discovery with Callibrity
Callibrity engaged with the testing facility to conduct an in-depth Problem Discovery focused on technician workflows and operational efficiency.
Our approach included:
- Observational reviews of facility operations and technician routines
One-on-one interviews with both internal and third-party technicians
Detailed process mapping to expose inefficiencies and points of failure
Collaborative ideation with stakeholders to propose high-impact solutions
Within weeks, our team identified eleven critical areas for improvement across technician workflows, process consistency, and system usability.
The Results

From Bottlenecks to Scalable Solutions
Callibrity’s discovery process delivered measurable outcomes:
- ️ 11 operational improvement opportunities identified and documented
- Deep understanding of technician pain points and workflow challenges
- Actionable recommendations to reduce cognitive load and streamline daily operations
- Development of three custom software solutions to automate processes, improve self-service capabilities, and minimize human error
Our partnership resulted in:
- Faster, more reliable facility readiness for testing
- Reduced manual effort and repetitive tasks for technicians
- Standardized processes across internal teams and third-party clients
- More efficient, intuitive error resolution procedures
- Significant reduction in avoidable operational costs
By modernizing technician workflows and optimizing operational processes, the facility is now better equipped to support its internal and external clients while maintaining its reputation for high-performance automotive testing.
Related cases
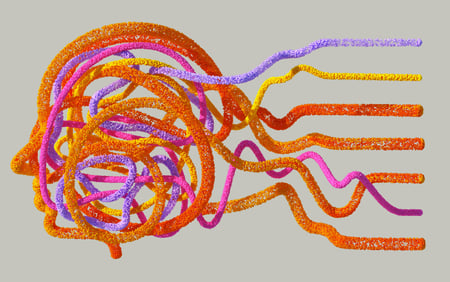
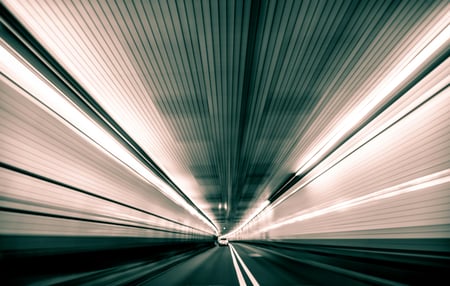
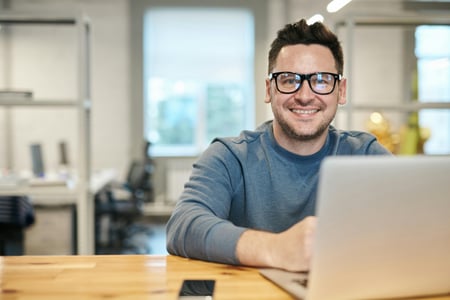